“Cumplimos”. Lo dice con una gran sonrisa ante un grupo de periodistas Marcelo Figueiras, presidente y principal accionista de Laboratorios Richmond, en la antesala de una visita a la nueva planta biotecnológica dotada de los últimos adelantos en materia de equipamiento para producir vacunas, anticuerpos monoclonales y otros productos biotecnológicos que está a punto de comenzar a funcionar en Pilar.
Nacida al calor de las urgencias de la pandemia, la escasez de insumos y las limitaciones en materia de vacunas, el entusiasmo de Figueiras es justificado, porque llevar a buen puerto este proyecto fue una verdadera tour de force. En el camino, se interpusieron la guerra con Ucrania, los vaivenes del virus y el cambio de gobierno. “Durante la pandemia se difundió el precepto de que ‘el que fabricaba vacunas vacunaba y el que no, esperaba’ –comenta el empresario–. Me propuse construir una planta porque es un seguro, nos da independencia sanitaria. Tuvimos propuestas de muchos países de Sudamérica para que nos instaláramos en esos lugares, pero creemos que nos debemos a nuestro país y a nuestros científicos”.
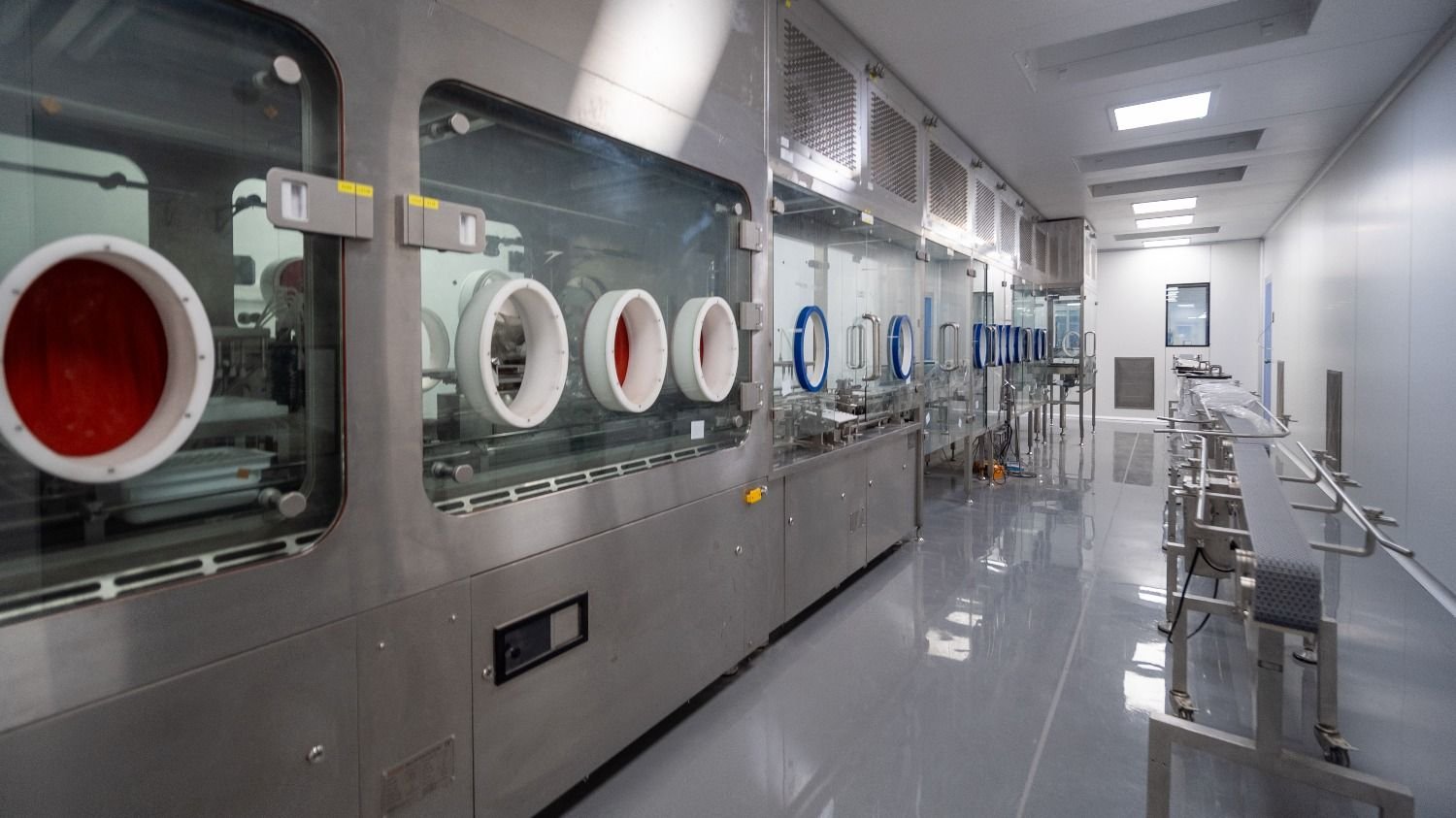
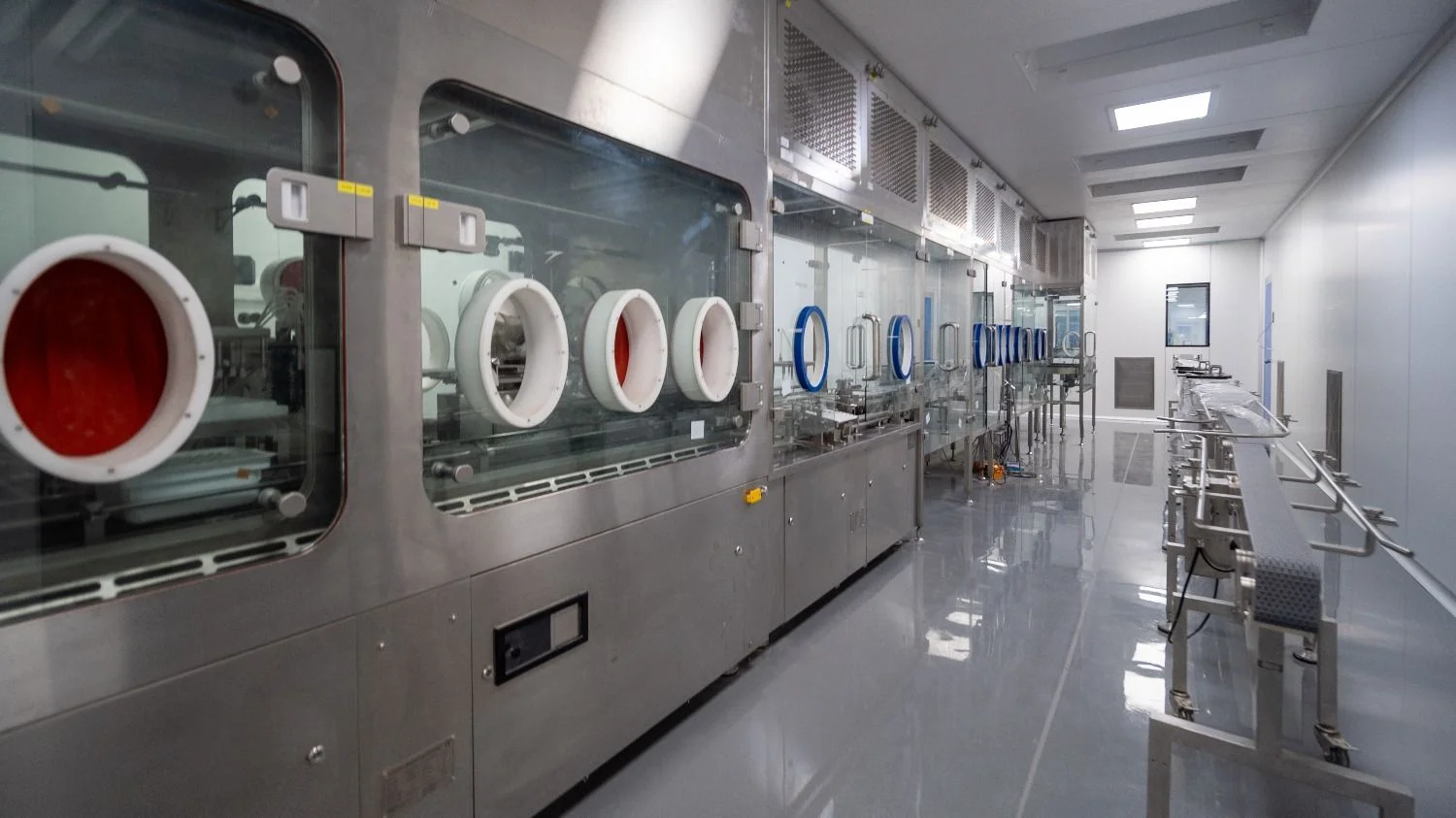
Este proyecto lo hacemos colectivamente. Sostené a El Destape con un click acá. Sigamos haciendo historia.
La construcción se financió a través de un proyecto desarrollado bajo el modelo de fideicomiso financiero, con la participación de más de 60 inversores públicos y privados de todas las orientaciones políticas, “inclusive un gran deportista, cuyo padre había fallecido de Covid”, comentó Figueiras. Exigió reunir entre 85 y 100 millones de dólares y “fue recaudado por el Banco Nacional de Valores con todos los controles que corresponden –aclaró–. La financiación estatal promueve el desarrollo de productos nuevos y a la larga vuelve al Estado en regalías
V.I.D.A. (Vacuna de Inmunización para el Desarrollo Argentino), como se llamó a la planta, es un centro de última generación de 11.000 metros cuadrados capaz de producir vacunas multiplataforma y distintos medicamentos biotecnológicos para Argentina y América Latina. Se estima que cuando esté funcionando a pleno, podrá producir unos 80 millones de viales y unas 28 millones de jeringas por año, dependiendo de las necesidades. Ya cuenta con acuerdos firmados para la producción de cinco vacunas (cuyos nombres deben mantenerse en reserva por razones de confidencialidad). El primero que sí puede revelarse se selló con CansinoBIO para la producción y comercialización de varias, entre ellas, Convidecia®, contra el COVID-19, para lo cual ya cuentan con la autorización de la Anmat.
Pero además de la fabricación, la planta se pondrá al servicio de la investigación y el desarrollo local, y ofrecerá a investigadores e investigadoras argentinos una plataforma para hacer transferencia tecnológica en una planta piloto con normas de buenas prácticas de manufactura (GMP).
En una construcción de pisos, paredes y equipos relucientes (la mayoría importados, salvo las calderas, fabricadas en el país) que aguardan la puesta en marcha, Nahuel Fernández, gerente de operaciones de Biotech, y Daniel Puyol, gerente de ingeniería y proyecto de VIDA, guiaron el recorrido por la planta, que destina 6000 metros cuadrados al área productiva, antes de que se cierre definitivamente a visitas y al personal que no esté específicamente acreditado por las estrictas condiciones de asepsia que es indispensable preservar.
El área “de servicios”, completamente separada de la de producción, alberga generadores eléctricos para que no exista riesgo alguno de cortes de electricidad, “manejadoras de aire” especiales para productos inyectables, y una planta de agua propia que asegura su limpieza y calidad. “El mayor porcentaje de nuestro producto es agua y tiene que cumplir con los más altos estándares nacionales e internacionales –explica Puyol–. Porque lo que se busca es que logre las certificaciones de todos los entes reguladores de la región y del mundo. Para eso, pusimos los mejores equipos disponibles, la almacenamos en tanques y la distribuímos en cañerías a 90° de temperatura”.
“La capacidad de generación de las calderas es de cinco toneladas de vapor por hora, la de aire comprimido, de 250 litros por segundo, y la de agua fría industrial, 400 toneladas de refrigeración [1.380.000 frigorías/hora]”, detalla Fernández.
En la planta baja de la nave productiva están instaladas 29 “manejadoras de aire” alemanas que garantizan la calidad, temperatura y humedad del aire que se inyecta en los sectores productivos. “La más grande mueve un caudal de 65.000 metros cúbicos por hora –subraya Puyol–. Es la que se encarga de acondicionar el depósito donde vamos a guardar materia prima o producto terminado para que se mantengan en condiciones”.
El equipo toma aire del exterior, lo enfría, lo lleva a una temperatura llamada “punto de rocío” para sacarle la humedad (gotitas en suspensión), y luego lo recalienta hasta la temperatura adecuada. El depósito tiene que mantenerse a alrededor de 24 grados y con una humedad menor al 70%. Y en la sala de producción, esos parámetros deben ser de unos 22° y menos del 60% de humedad. La misma máquina filtra el aire que se devuelve al exterior para evitar cualquier posible contaminación.
En un piso superior se ingresa a la planta piloto por un sistema de esclusas que aíslan las salas de presión diferencial, y evitan ingresos o fugas de potenciales contaminantes. Más pequeña, permite ensayar procesos y realizar desarrollos en lotes de baja escala. “El objetivo de esta área es por un lado recibir tecnología, y por otro desarrollar nuestros propios procesos y probarlos –explica Fernández–. Tiene un sector para preparación de medios de cultivo y soluciones, y salas libres para trabajar en lo que aparezca a futuro”.
En uno de los espacios, se conservan y amplifican las líneas celulares genéticamente modificadas para que produzcan proteínas específicas. “Se almacenan en tubitos en los que entran entre 10 y 20 millones de células –destaca–. Estos, a su vez, se guardan en tanques con hidrógeno líquido y capacidad para entre 500 y 1000 de ellos. Esas células se multiplican y generan la proteína de interés, que se purifica. El producto ya terminado se envasa en viales o jeringas”.
También disponen de un equipo para probar en paralelo ocho vasitos de 250 mililitros de cultivo en diferentes condiciones. “Así, cuando estemos desarrollando un proceso, podemos probar ocho fórmulas en simultáneo –dice Fernández–, algo muy importante porque con frecuencia puede ocurrir que pequeños cambios en las condiciones de cultivo o en la composición del medio alteren los parámetros de calidad del producto final, impidan su aprobación y exijan volver atrás”.
En la nueva planta se podrán producir inmunizaciones de diferentes plataformas, proteínas recombinantes y cualquier vacuna basada en adenovirus. También se podrá desarrollar la tecnología de vacunas de ARN, pero no producirlas en escala.
“Tenemos áreas preparadas para instalar la tecnología que crezca en el futuro –aclara Elvira Zini, directora de Asuntos Técnicos y Científicos de la compañía–. Y algo importante es que este sector también podremos usarlo para hacer lo que llaman ‘ciencia de traslación’. Puede venir un científico que necesite un lote chico para hacer una prueba de concepto en un estudio clínico y acá se lo podemos producir, cosa que a veces es un problema que tiene la ciencia argentina, porque o hay plantas de producción o hay laboratorios de desarrollo”.
En el área productiva, se pasa de biorreactores de 50 litros a grandes tanques de 200 y 1000 litros. “Una vez que ‘crecemos’ las células, estas liberan en el medio de cultivo la proteína que nos interesa, pero también impurezas, pedacitos de células y demás –subraya Fernández–. Eso lo tenemos que purificar y lo hacemos con el cromatógrafo, que inyecta el líquido de los reactores en columnas con resinas específicas a las que se adhieren esas partículas para alcanzar un 99,9% de pureza. También tenemos un equipo único en el país para desarrollar cromatografía continua que se está usando en los centros más avanzados del mundo y permite ahorros de hasta el 30% en una resina muy cara que se llama proteína A”.
La etapa final incluye el control de calidad: pureza, contaminantes, toxinas, esterilidad, pH [grado de alcalinidad] y otros indicadores que se miden para poder liberar los productos al mercado. “Usamos un espectrómetro de masas muy específico (cuyo valor ronda los 800.000 dólares) –cuenta Puyol–. No hay muchos instalados en la Argentina y menos en empresas. Nos permite no sólo hacer controles más específicos del producto terminado, sino también una mejor caracterización de los nuevos que queremos registrar y lanzar al mercado”.
Próximo a cumplir 90 años, Laboratorios Richmond es la primera compañía íntegramente de capitales nacionales que cotiza en la Bolsa de Comercio de Buenos Aires, y uno de los principales proveedores locales de medicamentos oncológicos y contra el VIH. A través de subsidiarias o socios estratégicos, sus productos se comercializan también en más de 26 países de África, Asia y Medio Oriente. Participa en estudios de investigación básica, en proyectos conjuntos con el Conicet y en ensayos clínicos en el país. Además, otorga las becas Sadosky para estudiantes sin recursos en las áreas de ciencias exactas.
“Tenemos un acuerdo histórico con una empresa de la India, Helero, con la que venimos trabajando en anticuerpos monoclonales desde hace años –concluye Zini–. Pero estamos negociando más y lo que es importante es que algunas de esas empresas quieren usar esta planta como base de su producción para Latinoamérica. Tiene la particularidad de que aquí se puede hacer el 100% del proceso [desde el desarrollo y los ensayos, hasta el escalado]. Hoy es la única del país que puede hacerlo”.